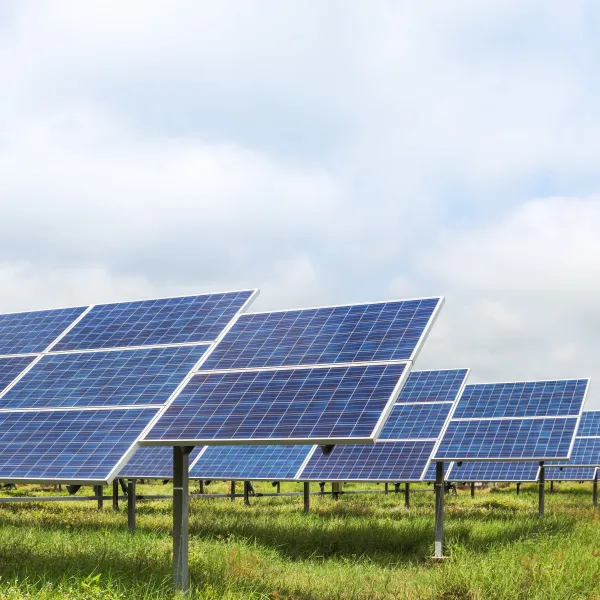
Blog Post
Helical Piles Help Keep Heavy Equipment Safely Supported On Large Solar Projects
Posted in Articles
While traditional foundations may settle with soil erosion, helical piles can provide a more reliable method for supporting solar inverters and other heavy equipment.
Heavy electrical equipment like central solar inverters is often installed on concrete foundations. But without additional support from below, the foundation can shift, causing equipment to rest unevenly. This puts stress on cables and can lead to diminished performance or even failures. Fixing the problem may require shutting down the entire solar array, and the resulting downtime reduces profits.
Helical piles (also referred to as piers or anchors) can provide a more stable foundation for heavy equipment. Piles are typically a slender metal shaft with a helix-shaped plate at one end.
Georgia-based Cantsink has been in business for 30 years and manufactures its own helical piles. The company discovered that the same piles used to stabilize home foundations and utility poles work just as effectively on solar projects.
Helical piles installed where an energy storage system will sit
"Helical piles are screwed into the ground, typically greater than 5 ft," said Lester Salinas, an engineer at Cantsink. "At this point, the soil is so compact that the structure is not going to undergo settlement. That's one of the primary reasons developers choose this method, to prevent that settlement."
Before starting a solar project, developers commission geotechnical site studies to examine soil types and determine if the location is prone to flooding. Developers can come to Cantsink with this information, as well as the weight and dimensions of the heavy equipment—central inverter, switchgear, battery bank, transformer, etc.—and the company will determine the number of piles and depth needed to support it. Sharon Lee, marketing director of Cantsink, said the company is a one-stop-shop for manufacturing and installation.
"We've got engineers that can specify the design, but then we can also install," she said. "People may not know exactly what they're looking for, [but] they know they need to stabilize the equipment for the life of the PPA. We can pull in site and soil details and what you're trying to do, and we can say 'Here's how to best accomplish this.'"
Salinas said that helical piles are self-verifying, meaning that by monitoring how much pressure it takes to install the pile, one can quantify the pile's load capacity. The more pressure it takes to drive the pile into the ground, the more load it can support.
"If you are not doing helical piles, you just hope the soil compaction was done well, but there's no guarantee," he said. "You hope for the best. But with helical piles, you have some sort of warranty that what was done in the field is going to last a long time."
An S&C system being positioned over helical pile foundations
Soil type determines how deep the piles must go. For example, sandy soil will require deeper piles. Flooding risk determines the elevation of the piles. If the site is in a flood zone, then piles are raised to the proper height to avoid water damage to electrical equipment.
Helical pile deep-foundation systems also ensure safety, remove easily and install quickly.
Quick installation was especially important to S&C Electric Company as it worked with a tight deadline for Ameren's microgrid facility in Champaign, Illinois. Located at Ameren's Technology Applications Center (TAC) near the University of Illinois campus, the Ameren microgrid provides multiple sources of distributed generation—solar, wind, natural gas and battery storage—to support the TAC and a 1-MW commercial and residential load.
"One of the hardest parts of the Ameren project was the schedule," said Paul Pabst, assistant manager of engineering services at S&C Electric Company. "We had our kickoff meeting in June 2016 and the system had to be completed by the end of the year. We knew we had to use something that would save time primarily, but using helical piles would also save cost."
The finished Ameren microgrid
Traditional heavy equipment foundations require hiring contractors to dig forms, or trenches, install rebar and pour in concrete. Then that concrete needs to cure. This can take days or weeks depending on weather conditions. Helical piles can be installed in a single day, and then a precast concrete or metal skid can be placed on top.
"We were able to quickly mount our control house, battery storage system and switchgear," Pabst said. "It was a success story because we were able to meet our deadline while keeping costs down."
Cantsink recommends installing helical piles at the start of a project, because retrofitting can be complicated and expensive. When retrofitting, the entire solar array must be shut down and getting the piles underneath a pad with existing wire and cabling can be cumbersome.
Lee said using helical piles has not yet reached common acceptance as a core strategy for long-term performance in solar installation development.
"More education is needed," she said. "EPCs are completely cost-focused, and I understand that. There are not a lot of margins in a solar project. But I think that the way a firm should look at this is you're trying to build a quality system for the life of the structure. This is the best way to protect the project's long-term performance and make sure it's going to be the best it can be."
For more information on Cantsink products and services, visit www.cantsink.com .
To read the original article from Solar Power World, click here.